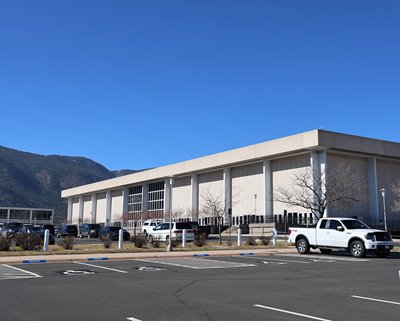
Cadet Field House at the U.S. Air Force Academy in Colorado Springs, Colorado, is undergoing a seven-year, $133-million renovation that includes new mechanical systems. SMACNA member Colorado Sheet Metal won a $5 million contract to replace the 1960s rectangular duct with spiral ductwork, along with other upgrades.
In its 55-year history, Cadet Field House has been home to some of the most competitive teams in college sports.
Spectators have watched U.S. Air Force Academy teams win regional championships in hockey and take part in the NCAA Division 1 basketball tournament.
One thing fans of the Air Force Falcons have never gotten to see, however, is a major renovation of the facility. Until now.
The field house, which is located at the U.S. Air Force Academy in Colorado Springs, Colorado, is undergoing a seven-year, $133-million project that will bring the facility in line with current NCAA Division 1 standards. In addition to a new roof, interior work includes new basketball court floors, renovated locker rooms, new dasher boards in the hockey arena and a modern running track. Energy-efficiency upgrades include LED lighting and sealing the building’s envelope.
As part of other efficiency improvements, the building’s 1960s mechanical systems are being replaced with high-efficiency air handlers, chillers and boilers. Geothermal HVAC is also being installed.
Colorado Sheet Metal, a commercial contractor based in Colorado Springs, Colorado, was awarded a $5-million contract to upgrade the field house air handlers and ventilation system that serve the spectator areas.
Replacing rectangular with spiral duct
CSM was tasked with replacing the facility’s 55-year-old rectangular ductwork with high-efficiency spiral duct above the hockey and basketball arenas, as well as in the indoor track and field area. In total, CSM installed more than 5,000 square feet of spiral duct.
Since CSM doesn’t have a spiral fabrication machine, it purchased the spiral duct from Prime Metal Products, a SMACNA contractor based in Gering, Nebraska.
While CSM could rely on an outside supplier to make the spiral duct, installing it was a different issue. In that case, Colorado Sheet Metal employees had to do it themselves — working from scaffolding 77 feet above the field house floor. They also had to do it when the hockey and basketball teams were between seasons.
Company President Gary Venable says it made for a “very challenging and unique” work environment.
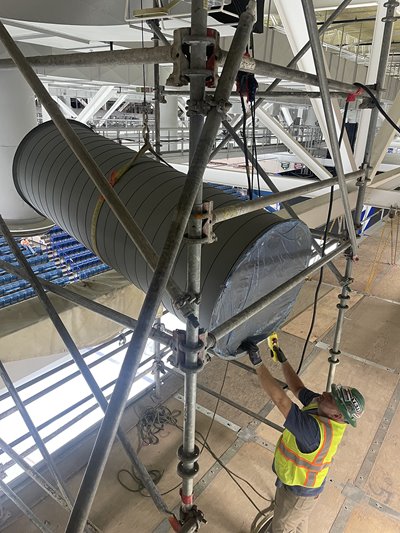
Colorado Sheet Metal apprentice Melissa Vigil (left) prepares to install the large diameter spiral duct with supervisor Jared Leblanc.
“We’re not able to use lifts or anything else,” he says. “We’ve built a hanging scaffolding system that hangs from the structure. We’re literally hanging and it’s probably 6 feet below the structure. We do all the work on that scaffolding.”
The scaffolding was approximately 40 feet wide, and it extended from one end of the basketball court to the other.
Venable says it took some time to figure out how to make it work.
“So, if you can imagine the joists and the beams, they’re literally taking chains and they’re hanging a platform below that structure,” he explains. And then we put another scaffolding on top of that platform to access our work. So, in this scenario, if you get added load onto the roof, like snow, which adds onto that structure, we cannot work there because if we put our stuff up there and our people up there, we would overload the structure.”
‘Making good progress’
Despite those challenges, Venable says the project has been going well.
“We’re fairly far into it,” he says. “We’ve completed all the duct over (the hockey arena) and all the duct over (the basketball court). We’re moving into the track area now. We’re making good progress on it. We’re probably 20% or 25% complete.”
As complicated as it has been installing duct from scaffolding, Venable says the project’s biggest challenge may be next year, when Colorado Sheet Metal workers will replace 19 outdated air-handling units with high-efficiency Trane models, plus 14 Cook exhaust fans.
It will mean more work in tight spaces 80 feet in the air.
“There’s a catwalk system above the arenas,” he adds. “I don’t even want to call it a mezzanine because it’s still a catwalk. It’s a graded system. And that’s where all the air handlers and fans go. And they’re large.”
Exactly when CSM will start that work depends on how the Air Force Falcons’ season goes. If the basketball or hockey teams make the playoffs, that could delay the expected June 2024 start.
“Air Force Academy has great athletic programs, and their hockey team is very competitive,” Venable says. “And the basketball team certainly can be as well.”
A special connection
As a third-generation sheet metal worker, Venable says he has a special connection to the Cadet Field House. In 1968, his father installed the rectangular ductwork that CSM workers are now removing.
“That was before I was born,” Venable adds.